Research project objectives/Hypothesis
The main aim of the project is development and extension of two dimensional concurrent multi scale full field model of microstructure evolution during thermo-mechanical treatment into the three dimensional space. Along with this, comparison of results from 2D and 3D models will allow to evaluate computational inaccuracies introduced by neglecting explicit influence of the third dimension in the microstructural full field models. The latter is crucial to exactly understand the influence of simplifications introduced by 2D full field models from the point of view of deterioration in results quality and gain in computational time resources. It is expected that obtained new knowledge will be the basis for the road map describing advantages and limitations of 2D/3D multi scale microstructure evolution models based on full field material representation concept.
Research methodology
The project is a close combination of numerical and experimental state-of-the-art techniques available and developed at the AGH University of Science and Technology. The numerical part of the project requires skills in numerical modeling and model development as well as access to the DMR and FE software. The Abaqus FE software is available in the AGH Cyfronet for the use in the current project on daily basis. However, most important from the project point of view is the recreation of microstructure for the FE simulation. This task will be done with the DMR methodology. At the current stage of the DMR advancement, it is a complete tool (DigiCore library), which allows creation of statistically representative material microstructure for the subsequent FE simulation (e.g. Abaqus). The DMR is an integral part of the project and will be extended to deal with investigated 3D microstructure morphologies. The PI has also a simplified in-house 2D SRX code that will be the basis for the present research. The crystal plasticity code used during the simulation is available through the cooperation with the UCL University. The code is already used at the AGH on a regular basis in various types of investigations. Developed models will be implemented using the object oriented C++, C# and classical Fortran programming languages. The Visual Studio2016 will be used as a programming environment. The C++ and Python will be used to incorporate the DMR model into the finite element software and for development of data transfer algorithms between FE and CA.
The experimental part of the research will also be realized at the AGH University. The PI and his team have direct access to the optical and scanning electron microscopes, electron back scattered diffraction detectors, in-situ tensile stage with heating capability. The part related with micro pillar compression tests will be performed free of charge at the Deakin University.
Research project impact
The 3D combined finite element and cellular automata (CAFE) model will be developed within the project. Numerical simulation of the static recrystallization of microstructure after large plastic deformation is selected as a case study for the investigation. The finite element method will be used to evaluate mechanical response of digital microstructure to loading while cellular automata will be used to predict corresponding microstructure evolution. Particularly valuable aspects of the project are related to development of mechanisms for boundary condition transfer between macro and micro scale FE models, development of smoothing algorithms for conforming FE meshes, evaluation of representativeness aspects of 3D digital material representation models, development of data exchange mechanisms between 3D FE DMR models and CA code, development of fully 3D cellular automata model of microstructure evolution at elevated temperatures, efficient implementation of the 3D CAFE model algorithms for execution within acceptable computing times, identification of hardening behaviour of particular grains at room and elevated temperatures, and finally, development of the road map describing advantages and limitations of 2D/3D multi scale microstructure evolution models based on full field material representation concept.
To summarize, the full field methods can also provide detailed description of material behaviour in the conditions difficult to monitor experimentally. As a result, these models are often used to develop simplified mean field approaches for practical applications. In that way amount of time consuming and expensive laboratory investigations, required to develop such mean field approaches, is significantly reduced.
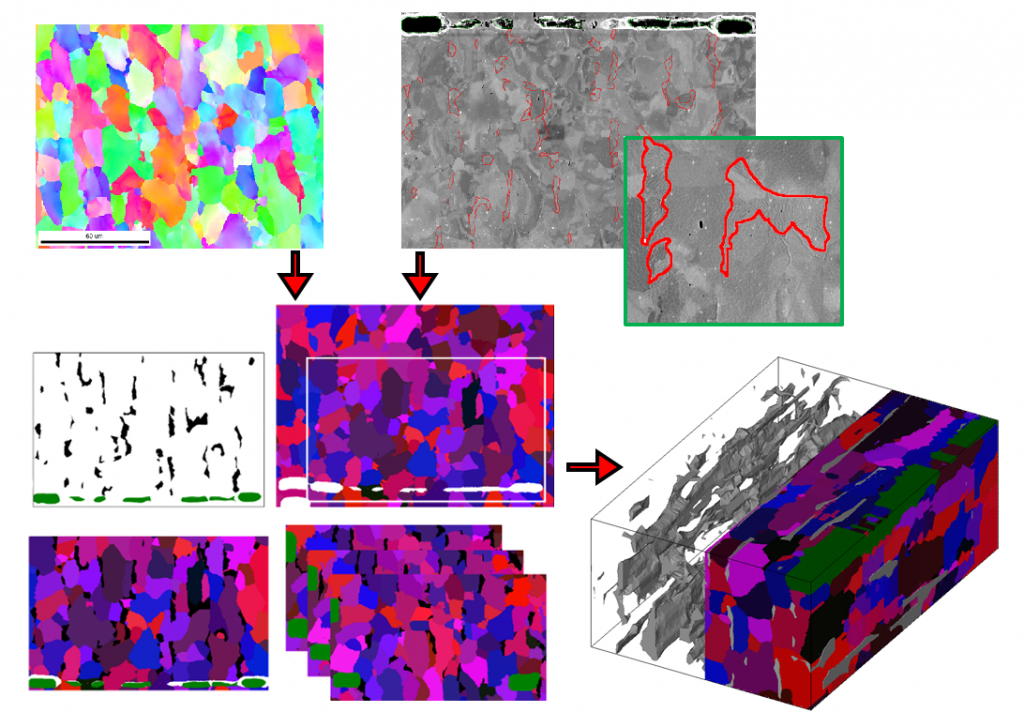